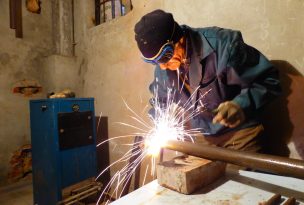
日本の産業界を力強く支えてきた製造業。
しかし、働き手の人数が減少し、熟練技術者の高齢化が課題となっている今、製造業はかつてないほどの危機を迎えています。
そうした中、期待されているのがIoT(Internet of Things)を活用した、技能技術の伝承です。
では、具体的にどのような可能性があり、その実現に向けては何が必要なのでしょうか。本記事では、実際の事例を通じてご紹介していきます。
熟練技術者が退職…工場から技術が失われつつある
以前より製造業の現場では、技術者の高齢化が課題視されていました。そして昨今、その課題はより顕在化したものとなり、企業経営の現場に影を落としています。
高齢化による定年退職
経済産業省の調査によると、2025年までに経営者が引退平均年齢を迎える中小企業のうち、約半数は後継者がまだ決まっていないとされています。これはすなわち、これから数年~10年間のうちに、日本の製造業の約半分が存続の危機に直面することを意味しています。
この危機的状況は、定年退職が相次ぐ熟練技術者にも共通しています。専門性の高い各社独自の技術は、その担い手が失われたとき、姿を消してしまう恐れがあるのです。そして、この状況をなかなか打開できない背景にみられるのが「若手人材の採用難」です。
若手の採用ができない
少子高齢化に拍車がかかる今、日本の労働力人口は減少傾向にあります。そうした中、製造業による若手人材の獲得は困難を極めています。
その要因として考えられるのが、製造業の現場に対する3K(きつい、汚い、危険)というマイナスイメージ。工場などで汗だくになって働くイメージや、危険を伴う作業が多い印象を持つ方は依然として多いようです。
それに加えて、90年代に訪れたバブル経済後のリストラは、製造業へのマイナスイメージにつながったといわれています。同時に、欧米や中国といった海外メーカーと比較すると技能人材の待遇が低いことも、人材確保に苦労する一因といえそうです。
こうした人材市場を踏まえたとき、新たな人材を採用するよりも、現場で勤務している人材の教育を充実させ、離職を防ぐことのほうが現実的なアプローチといえます。そのような視点で見たとき、製造業の現場における教育体制にも、改善すべき点が見えてくるはず。ここで着目したい点が、教育・指導方針に関する課題です。
教える内容が体系化されていないため教育ができない
製造業の現場では長らく、「技は見て盗むもの」という職人気質の考え方が重視されてきました。しかし、この考え方の下では、数十年単位での下積みが求められます。そして、体系的な考え方に基づいて順を追って教えるような指導法は、決して良いとはされてきませんでした。
しかし、多品種少量生産にみられるような機動的な生産スタイルでは、この考え方がベストとは決していえません。市場の変化が激しい時代に業績を上げるためには、いかに早く技術の標準化を図り、それを素早く横展開するかが鍵を握るからです。
こうした理想の姿と現実のギャップを埋めるためには、どのようなアプローチがあるのでしょうか。その解決策として挙げられるのが、IoT(Internet of Things)の活用です。
IoTが助け船に。業務の標準化/技術伝承
IoTの活用を考える時、ポイントとなるのがセンサーによる情報の定量化です。これは例えば、センサーによって機器の状態を判断したり、製造過程を数値化して示したりすることを意味します。
具体的には次のような事例が挙げられます。
業務の「平準化」をするIoT活用例
1つ目は、設備点検にIoTを活用した事例です。
従来、従業員が目視で行っていた機器の稼働状態のチェック。ここにIoTセンサーを活用することで、現場の従業員は、センサーが読み取った数値の判定を画面上で行うだけで済むようになります。また、AR(拡張現実)などの技術を組み合わせれば、点検対象の設備にゴーグルやタブレットをかざすだけで、複数機器のチェックを一目で行うことが可能になります。
このような仕組みを活用すれば、属人化していた業務を誰が担当しても同じレベルで実行できる業務に変えることもできるでしょう。こうした取り組みは、従業員ごとの経験の差を埋めるヒントとなるはずです。
工場の「技能伝承」をするIoT活用例
2つ目は、属人的な業務を数値化、マニュアル化する取り組みです。
例えば、熟練技術者の視線の動きを見える化して形式知に変える、視線追跡機能付きヘッドマウントディスプレイ。この技術を活用し、細かな目線と手の動きをデータ化することができれば、従来は言葉にして伝えることが難しかった技能を伝承することが可能になります。
熟練技術者の手と視線の動きを一体的に捉えてデータ化できれば、蓄積したデータを基に技能訓練マニュアルを作成することも可能になるはず。こうした取り組みは、職人の視界をデジタル化できるIoTの力があってこそ実現できるものといえるでしょう。
IoT導入は、データのプラットフォーム構築から始まる
前述の事例は、いずれもIoT技術をベースにしつつ、AI・ARによる映像処理技術が組み合わさって実現しています。そして、このような拡張性を可能にするうえで重要になるのが、センサーやビーコンといったデータを収集の仕組みと、データを一元管理するプラットフォームの構築です。
テックファームでは今回ご紹介したような、新たなIoT活用の全体構想からプラットフォームの設計・構築、システムの開発、運用支援までをワンストップで行っています。また、「まずは小さな成果を積み重ねたい」といったPoC(概念実証)のご要望にお応えすることも可能です。
従来のIoTソリューションは、導入までに一定以上の時間や費用を要すものです。しかし、導入段階で手間をかけると、実証実験で得ておきたいデータの蓄積が不十分に終わってしまう恐れがあります。だからこそ、IoT導入には手間をかけず、スピーディーにPoCを実行し、少しでも多くのノウハウを社内に蓄積することが大切といえます。
テクノロジーを活用し、技能伝承の実現に向けた一歩を踏み出したいとお考えの企業様は、ぜひIoTの活用をご検討ください。