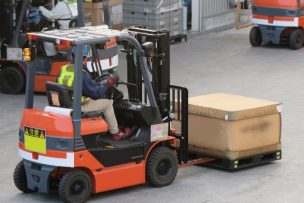
物流倉庫、工場、建設現場などで製品や部品、資材などを日々大量に運搬しているフォークリフト。
日本国内に現在100万台あるといわれていますが、IT化が叫ばれる昨今もフォークリフトを使った作業にはまだアナログな部分が多く、コスト削減や効率の改善の余地が多く含まれています。
本記事では、フォークリフトに関わるコストや稼働効率の改善について、今注目されているIoTを活用したソリューションを交えてご紹介していきます。
フォークリフトにまつわる3つのコスト
最初に、フォークリフトを活用する上で発生するコストを細分化して見ていきましょう。
フォークリフト自体のコスト
まずわかりやすいのが、フォークリフトの車両自体にかかるコストです。車両代金以外にも、1台所有するだけでもかなり多くのコストが発生します。車両にかかるアタッチメントやオプション設定、燃料費用やメンテナンス費用、保険代など、維持費がかさむものです。
フォークリフトを動かす・管理する人件費コスト
フォークリフトを動かせる人がいないと話は始まらないのですが、今この人件費が高騰しています。リクルートジョブスの発表によると、2018年1月の三大都市圏における「構内作業(フォークリフト等オペレータ)」のアルバイト・パート募集時平均時給は1,159円となっており、昨年同月比の5.2%増と最も増額している上位3職種にランクインしています。
昨今、物流のドライバー不足が度々メディアに取り上げられますが、実は倉庫内の労働力不足も深刻化しているのです。オペレーターの労務や勤怠にかかるコストも考えると、人件費は決して無視できない大きなコストです。
フォークリフトによる事故と事故予防コスト
フォークリフトを扱う現場では、過去3年で毎年2,000件弱の人身事故が発生しており、その内の毎年30名近くが残念ながら命を落としています。(陸上貨物運送事業労働災害防止協会発行「陸運と安全衛生 」より)
現場で労働災害が一度でも起これば、直接損害だけでも数千万円の損失見込みになります。もちろんそれだけでも大きな損失ですが、お客様の品物が破損ということも重なれば、企業間の信頼を失うリスクも表面化し、事故のリスクは大きいものとなります。そのため、事故予防が重要となり、それにもまたコストがかかります。
フォークリフトの稼働効率の改善は現状分析から
ここまでに挙げたコストやリスクですが、近年は対策の仕方が変化してきています。各社、フォークリフトの性能の向上に力を入れるのではなく、工場や倉庫そのものの運用の効率化に着目しているのです。この章では、フォークリフトの運用をどのように効率化していくのかをご紹介していきます。
現状の動線把握の仕方
改善を進めていくためには、まず現状を知ることが大事です。今フォークリフトがどのような動線で動いているのかを俯瞰して見ることで、稼働効率を下げている場所や時間帯、オペレーターを把握でき、改善すべきポイントが明確になります。
最近では、IoTを取り入れて動線把握するのが主流となっています。フォークリフトに位置情報を発信するビーコンを付け、現場のあらゆる箇所に受信機を設置することでフォークリフトの位置履歴データを取得する方法です。
この手法を活用することによって、フォークリフトに限らず工場や倉庫などの屋内のあらゆるモノや人のリアルタイムな位置情報や動線履歴を、時間や人的コストをかけずに収集することが可能になりました。収集したデータに関しても、クラウドベースで管理ができるので、企業の導入ラインもかなり下がりました。
フォークリフトの動線把握によって見えてくるもの
混雑による稼働効率低下
動線を見える化すると、フォークリフトが頻繁に往復して渋滞が起こりやすい場所や時間帯、逆に空きやすい場所と時間帯が見えてきます。混雑時はフォークリフトの移動スピードが低下したり事故が発生しやすくなったりと、稼働効率低下に繋がります。目的地までのルートや現場のレイアウトを変更するなどの対応を取ることで、混雑が解消でき、効率の改善につながるのです。
無駄な動線による稼働効率低下
同様に、フォークリフトの遠回りや無駄な往復も簡単に把握できるようになります。在庫置場や部品の保管場所が最適化できてないゆえに、フォークリフトが回り込みを余儀なくされていたり、部品の補充などの情報共有が足りずに一往復でできるものを複数回往復して対応しているといったケースはよくあることです。最大限の荷物を同じリソース内で移動させるには、こういった無駄な動線を無くしていく必要があります。
コスト削減につながるIoTの使い方
フォークリフトの台数削減
現在多くの企業でフォークリフトそのものの台数を減らす、又は見直す動きが見られ始めています。IoTを取り入れることで、無駄な動線や非稼働時間の可視化ができ、フォークリフトの台数を減らしても作業に支障がないことが証明できるようになりました。フォークリフトの台数を削減できれば、車両にかかる維持費やそれを動かす人件費の削減に繋がります。
無駄・危険な動線改善で作業員の稼働効率も改善
IoTで動線分析の精度を高めることで、そこで働くオペレーターの作業工程の簡略化やリスクを最少限に抑えることが可能になります。今まで人力や目視で行なっていた作業が自動化され、経験値に左右されず作業フローが最適化され、現場全体の状態把握ができると、取れる対策の幅は広がり、より高いパフォーマンスを出せるようになります。
まとめ
人手不足や人材の定着が問題視されている現在、倉庫・工場内の業務効率化は避けられないテーマとなりました。
機械の性能を高めるのはもちろんの一つの手段ですが、データ収集・分析を経て見えてくる”無駄”を解消させることで効率がよくなり、結果コスト削減に繋がったといった例は続々と出てきています。
持続性のある改善を図るためにも、まだIoTの導入を検討されていない方は、まずは他社事例などを聞いてみることから始めてみてはいかがでしょうか。