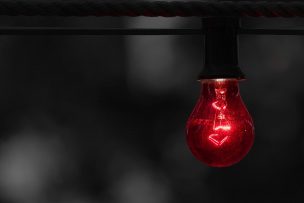
IoT(モノのインターネット化)技術の発展が続く今、その応用が最も進む業界として製造業が挙げられます。
なかでも注目を集めているのが、収集したデータによって設備機器のトラブルの予兆をいち早く察知し、生産性向上に役立てる「予防保全」の取り組みです。
今回は、IoTを活用した予防保全の概要と導入の流れについてご紹介します。
IoTによる工場の稼働停止予防とは?
高い生産性が求められる製造業の世界において、工場の稼働停止は例え短時間であっても大きな損失です。生産計画を狂いなく実行するためにも、トラブルを先回りして回避する「予防保全」の取り組みは必須要件といえるでしょう。
予防保全という考え方が広まるまでは、機器設備が故障してから対処する「事後保全(RM:Reactive Maintenance)」が一般的でした。しかし、突然の故障による機器停止は直近の生産計画に影響をもたらすのみならず、顧客からの信頼失墜につながることから、いまでは多くの工場で見直しが図られています。
このような背景で普及したのが、部品ごとに耐用時間や交換時期を定めたうえで、一定期間使ったら故障していなくても交換する「予防保全」の取り組みです。一方、現場のコスト削減が急務になる中では、予防保全に伴うコスト増も大きな懸念点となります。
これらの理由から、稼働停止予防のためにセンサー技術とIoTを活用してメンテナンスコストの最適化を目指す企業が増えているのです。
機器の予防保全をIoT化するメリット
IoTセンサーで収集した設備機器の稼働ログや異音などのデータを分析すれば、人間が気づかないような小さな異常を見つけることが可能になります。こうした仕組みを活用して予防保全をIoT化することは、製造業の現場においてさまざまなメリットがあります。
メリットの一つとして挙げられるのが、設備機器に関する「異常の早期発見」です。
小さな異常を発見し次第、適時対応を行うことで、メンテナンス対象を絞った無駄のない設備保全活動が可能になります。
もう一つのメリットが、保全に関わる「人員コストの削減」です。
一定期間ごとに予め決まった点検項目に沿って実施する方法では、3ヶ月・6ヶ月・1年に1回といった形で一定のマンパワーがかかります。定期点検の必要性が完全になくなるとは限りませんが、予防保全のIoT化によって保全活動のメリハリをつけることで、一定の人員コスト減を行うことができるでしょう。
このように品質・コスト・業務効率化といったさまざまなメリットが挙げられる予防保全のIoT化ですが、その導入の流れ見てみると、大きく分けて5つのステップが存在します。
IoT導入と予防保全の開始までの進め方
1つ目のステップで行うことは、データの取得です。ここでは最適なセンサーの種類を特定し、取り付け位置を決定。同時に、取得するデータの有用性を検証すると共に、実運用を想定したデータ収集の仕組み化を行います。
2つ目のステップは、データの前処理です。ここでの処理とは、取得したデータを活用しやすい形に変換したり、加工したりすることを意味します。AIを活用するならば、ここで機械学習にかけるための変換処理を行うこともあります。
3つ目のステップでは、処理されたデータの結果に応じて、適切なアラートを出す仕組みをつくります。もちろん、最初に設定されたアラートが現場環境に最適化されていることは稀でしょう。だからこそ、蓄積されたデータをもとにして、そのタイミングをチューニングしたり、AIを活用して絶えず精度を高めたりすることが大切です。
以上のように、予防保全のIoT化には、センサーによるデータの取得からアラート、保全作業まで、さまざまな準備を行う必要があります。そして、これらの環境を用意する上で最も重要になるのが、センサー情報を一元管理するプラットフォーム環境です。
センサー情報を一元管理するIoTプラットフォーム
IoTでの予防保全を実現するためには、複数の機器に取り付けられた複数のセンサーを活用します。そのため、複数のセンサーから集約した情報を一元管理できるプラットフォームの構築が欠かせません。
こうしたプラットフォームの構築には、IoTやセンサー技術とは異なる知識やノウハウが求められます。また、実際の製造現場で環境を構築しなければ見えてこないネットワークなどの課題もあるため、まずはスモールスタートでトライアルを行い、その結果を踏まえて次のステップを進めていく必要があるのです。